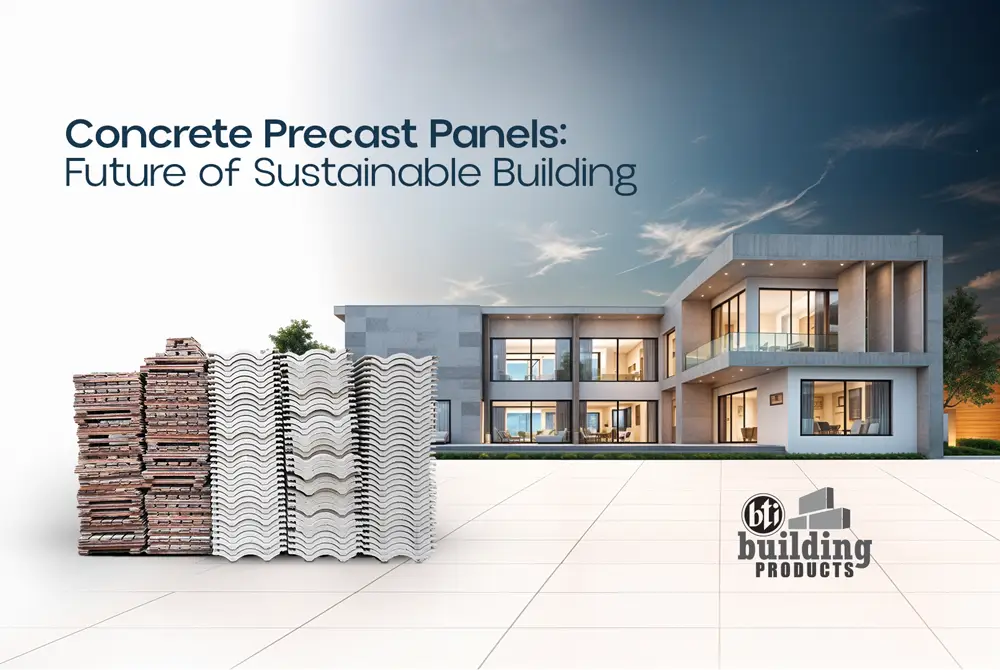
Concrete Precast Panels: Future of Sustainable Building
So what is a Concrete Precast Panel?
A pioneer in the real estate industry of Bangladesh, bti has always striven to be innovative in the structures it creates. We took the first steps towards green, sustainable architecture by introducing concrete hollow blocks in construction – not only would these be manufactured by bti building products, but they would undoubtedly lay the groundwork for other companies to explore the arena of sustainable architecture. This would be good for the environment and future generations, yes, but also would be very cost-effective in the long run, saving each organization a lot of money in terms of production and transport costs.
After a few years and extensive research & development, the precast concrete panels using foaming agents were introduced late last year. The Aqualuna project is the first project of bti that is using this revolutionary product. The concrete precast panels are made at the site, which means it saves money on manufacturing plant, transportation and storage of the materials. Since there is the use of foaming agents in the making of the products, the resulting panels are lightweight, leading to a finished structure that will be up to 40 to 50% lighter than if the same building were constructed using concrete hollow blocks.
Since there will be no need for manufacturing plants as the panels are produced on site, customizing the size will be much easier than it used to be. There will also be even lesser pollution as the manufacturing happens on site, requiring some very basic items to create a truly extraordinary product. The molds for the panels are created at very low cost, and then used to form the precast panels. Rods are inserted into preformed holes in the panels. Then the concrete is mixed with the foaming agent and poured into the molds. When the concrete is half set, the rods are taken out to create gaps or hollow spaces in the panels. These are then used in place of concrete hollow blocks. As mentioned before, using these panels in construction have a number of advantages. Other than minimized transport, storage and production costs; using these panels is going to be sustainable and cost-effective in the long run. The architect or designer of the project in question can customize sizes and shapes to best suit the project.
A major advantage of the precast concrete panels is their thermal mass, otherwise known as the ability of structures to release and absorb heat. Buildings using precast concrete panels will have consistent interior temperatures, lowering the need to heat and cool the entire building. The hollow panels allow for natural regulation of the temperature, meaning that during the life cycle of the building; a large amount of energy (and thereafter costs) will be saved on HVAC systems.
Compared to all other traditionally used building materials, the precast concrete panels produce less waste and reduce the carbon footprint too. Workers can measure how many panels will be needed for each structure, and then make the appropriate number of panels necessary to complete the project. Concrete is also the strongest building material available. Precast panels offer increased protection against the weather, allowing buildings to last much longer, as well as lowering the need for maintenance & repairs.Precast concrete panels are also highly recyclable. Once their useability has ended, they can be broken down and reused to produce other building materials (like gravel). This would, in turn, allow us to reduce the amount of wastage that is sent to garbage dumps and landfills.
Precast concrete panels are made in a very precise manner, meaning that they require minimum reworking & repairs. This, in turn, will lead to greater cost-effectiveness in the long run. Since the precast concrete panels are made at the site of the project, the scope for far better quality control exists, and the end product is far superior than the concrete hollow blocks previously produced by bti building products. Due to the availability of customization of the precast concrete panels, there is less chance of defects in the end product. This, then , means that the overall quality of construction of bti will now be higher than it previously was.
No matter what kind of architectural styles or materials you use, there should be at least some creative freedom that the architect might be allowed to explore and express freely. It is absolutely essential that the project be aesthetically pleasing, but also fulfilling its basic purposes. These days, both simple and intricate details can be incorporated with little to no prior training provided. Precast concrete panels are strong and can withstand weather of any kind, be it storms, hail or even earthquakes. Their durability and long-lasting nature is one of the reasons why many construction and real estate companies in Bangladesh are switching over to this product.
In the coming days, precast concrete panels will play a significant role in shaping the future of sustainable or green architecture. Further advances in technology will allow for the use of low-carbon cements, as well as renewable systems like green roofs & solar panels. Precast concrete panels are not just a passing trend for builders, developers & architects. Rather, they are on their way to taking a surefooted step into building a more durable and purposeful future, and a greener tomorrow.